As technology rapidly advances, the Southern United States has emerged as a key player in the burgeoning advanced manufacturing industry, with growth driven by a skilled workforce and strategic investments in research and development.
One notable case study is Analog Devices—a global leader in digital and analog component manufacturing— which aimed to consolidate multiple regional locations into a single, cohesive facility within North Carolina’s Research Triangle Park. The objective was clear: to repurpose an existing campus into a progressive environment tailored for engineers and technicians known as the Analog Devices Regional Operations Facility.
Facing space limitations and intense programming systems infrastructure needs, the project demanded an overhaul of existing mechanical, electrical and plumbing (MEP) systems to boost efficiency and meet rigorous programmatic requirements.
Promoting Business Continuity with Robust Backup Systems
The facility’s ground floor hosts more than 300 lab benches for designing, developing and testing a wide range of high-performance analog, mixed-signal and digital signal processing circuits. Given the critical nature of these industrial operations, meticulous planning of MEP infrastructure was essential to accommodate the vigorous building system demands, which involved strict temperature and humidity control needs.
To address this, we implemented advanced heating, ventilation and air conditioning (HVAC) solutions, featuring redundant systems to prevent space environmental conditioning failures during prolonged sensitive electronic testing sessions. Dual HVAC units were also deployed to double capacity, seamlessly transitioning to backup equipment in the event of failures, thus safeguarding uninterrupted workflow and bolstering resilience against productivity losses.
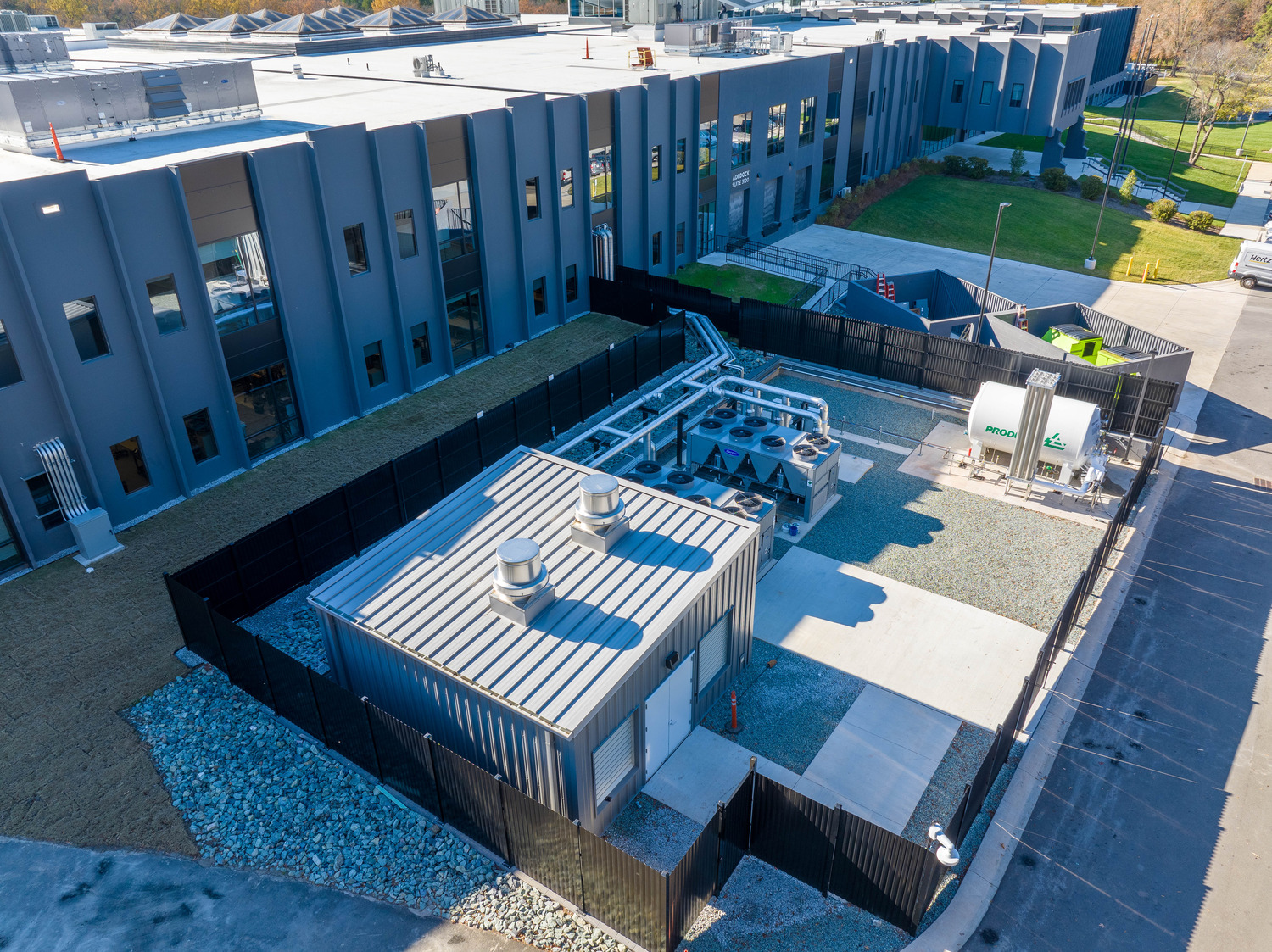
The mechanical yard features an industrial air compressor building, nitrogen storage and air-cooled chillers for both comfort and process cooling.
Utilizing “Green” MEP Strategies for Energy Savings
In line with long-term sustainability goals, stakeholders prioritized designs that contribute to increased energy savings. Variable speed air and hydronic HVAC systems, eco-friendly LED lighting fixtures were some of the measures integrated throughout the 140,000 sq. ft. facility to mitigate energy consumption while fostering employee comfort.
Moreover, the layout incorporates robust infrastructure to support specialized equipment, including liquid and gas nitrogen, vacuum systems and process chilled water, crucial for maintaining precise testing conditions at temperatures as low as -270 degrees Celsius.
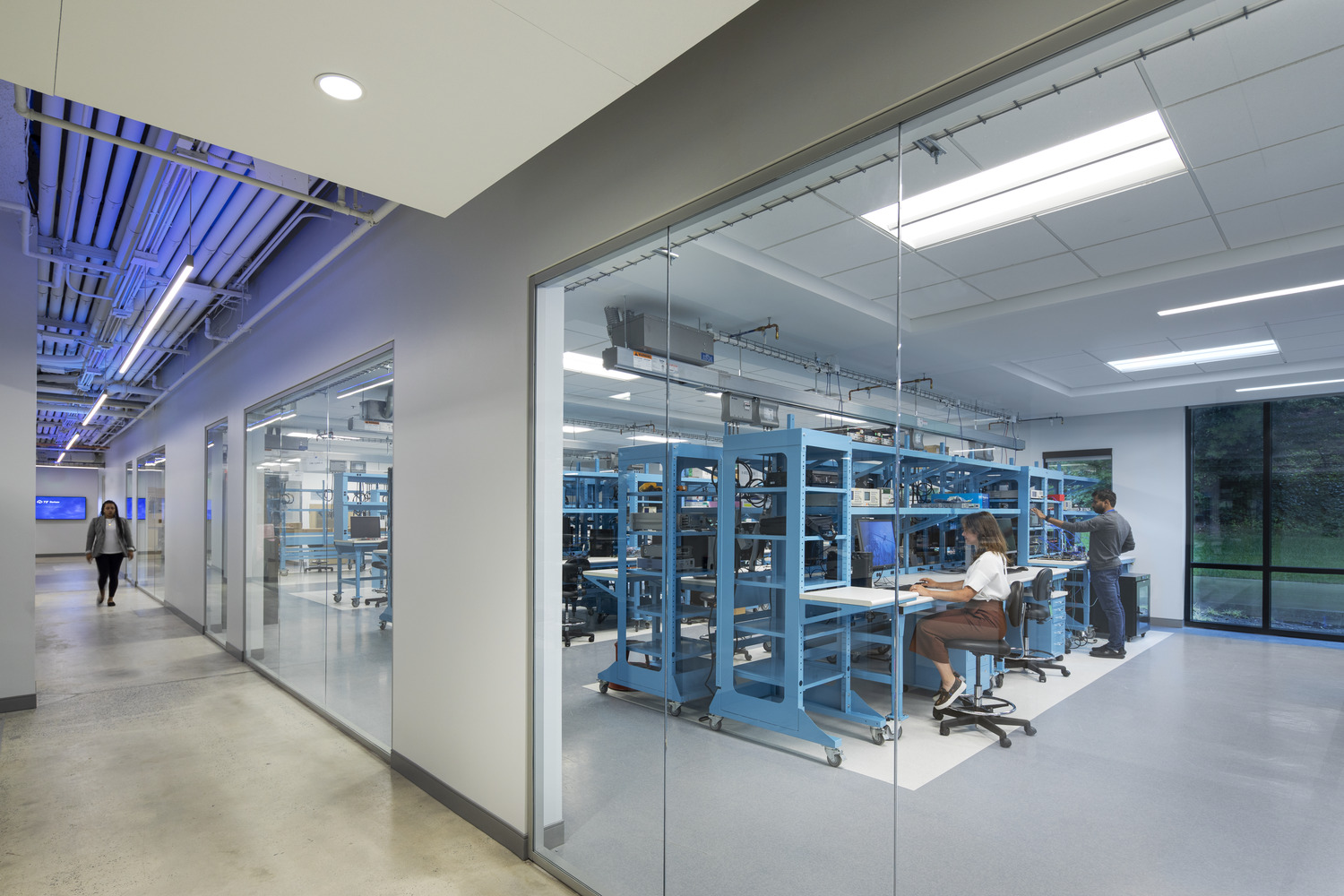
In the bench labs, overhead electrical busbars were installed to facilitate easy and flexible connection of testing equipment, streamlining power distribution while minimizing material usage and energy waste associated with multiple individual outlets.
Reducing Carbon Emissions with Electrified Systems
The unique dual HVAC systems were also tailored for full electrification, upholding environmental stewardship and financial prudence. By harnessing electricity to drive HVAC functions, these systems stand in contrast to their non-electrified counterparts, which rely predominantly on fossil fuels like natural gas or oil. As a result, they eliminate local carbon emissions—providing clean, energy-efficient operations that lead to heightened indoor air quality and decreased maintenance needs.
Cradle to cradle carbon neutral material selections were also utilized to complement these systems and further reduce the facility’s carbon impact.
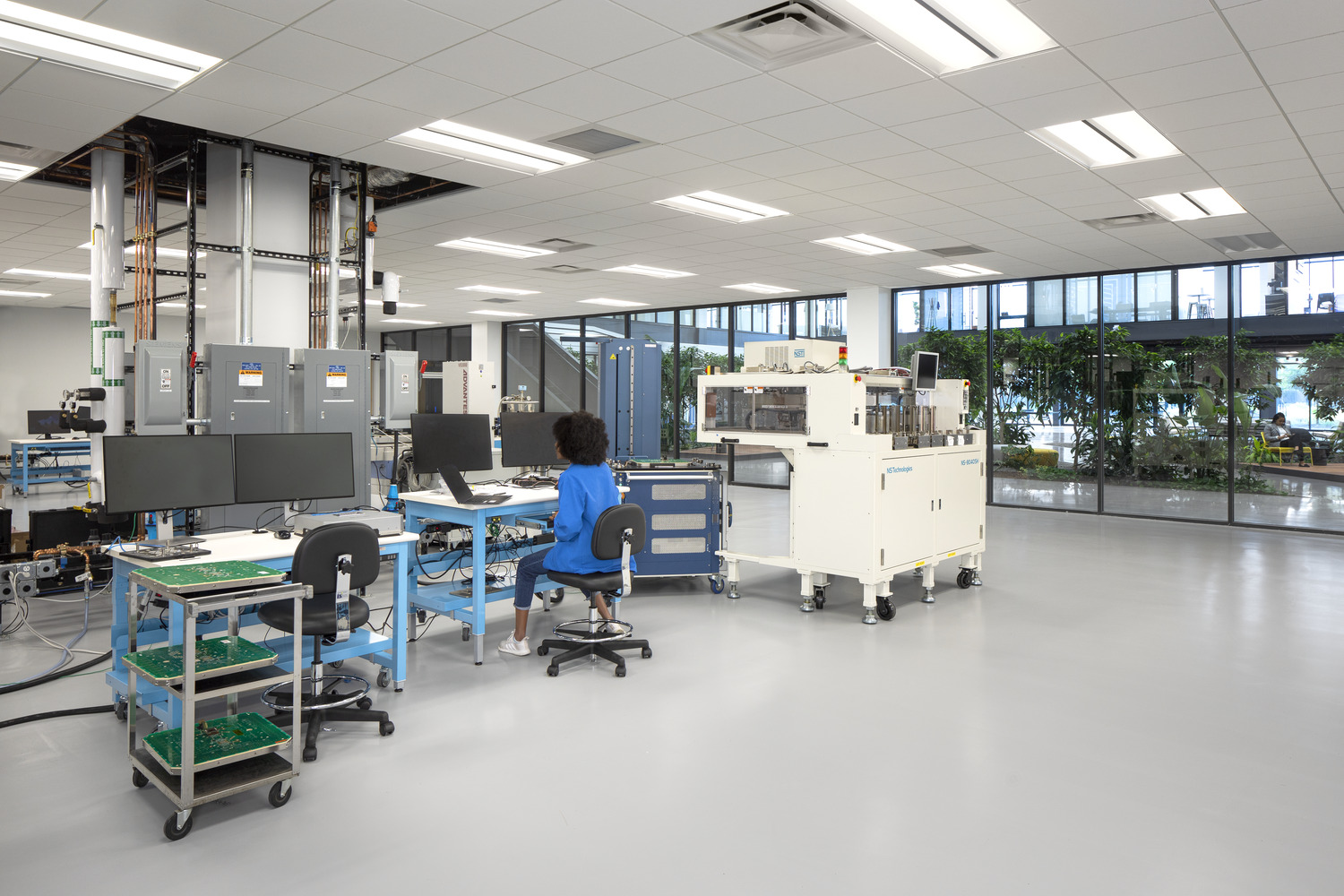
Heavy electrical and compressed air systems were included throughout the interior.
Operational Excellence, Redefined
By prioritizing flexible and highly sustainable MEP design, the updated campus not only meets Analog Devices’ complex infrastructure requirements, but also lays the groundwork for long-term success and expansion. This forward-thinking building systems approach has led to a more adaptable and resilient work environment, capable of responding to—and even shaping—evolving industry standards.